John K. Philips
Our Latest Blogs
Based in St. Helens, we are one of the longest established transportation companies in the Northwest – we’ve been doing this for over 40 years now. Here at John K. Philips Group we don’t believe in a one size fits all approach to transport and distribution, which is why we have earnt a reputation over the years for excellence. We understand that no two operations are the same and go above and beyond to offer you the exact support your business needs to thrive. With our ISO 9001:2000 quality accreditation, you can expect a high level of professionalism.
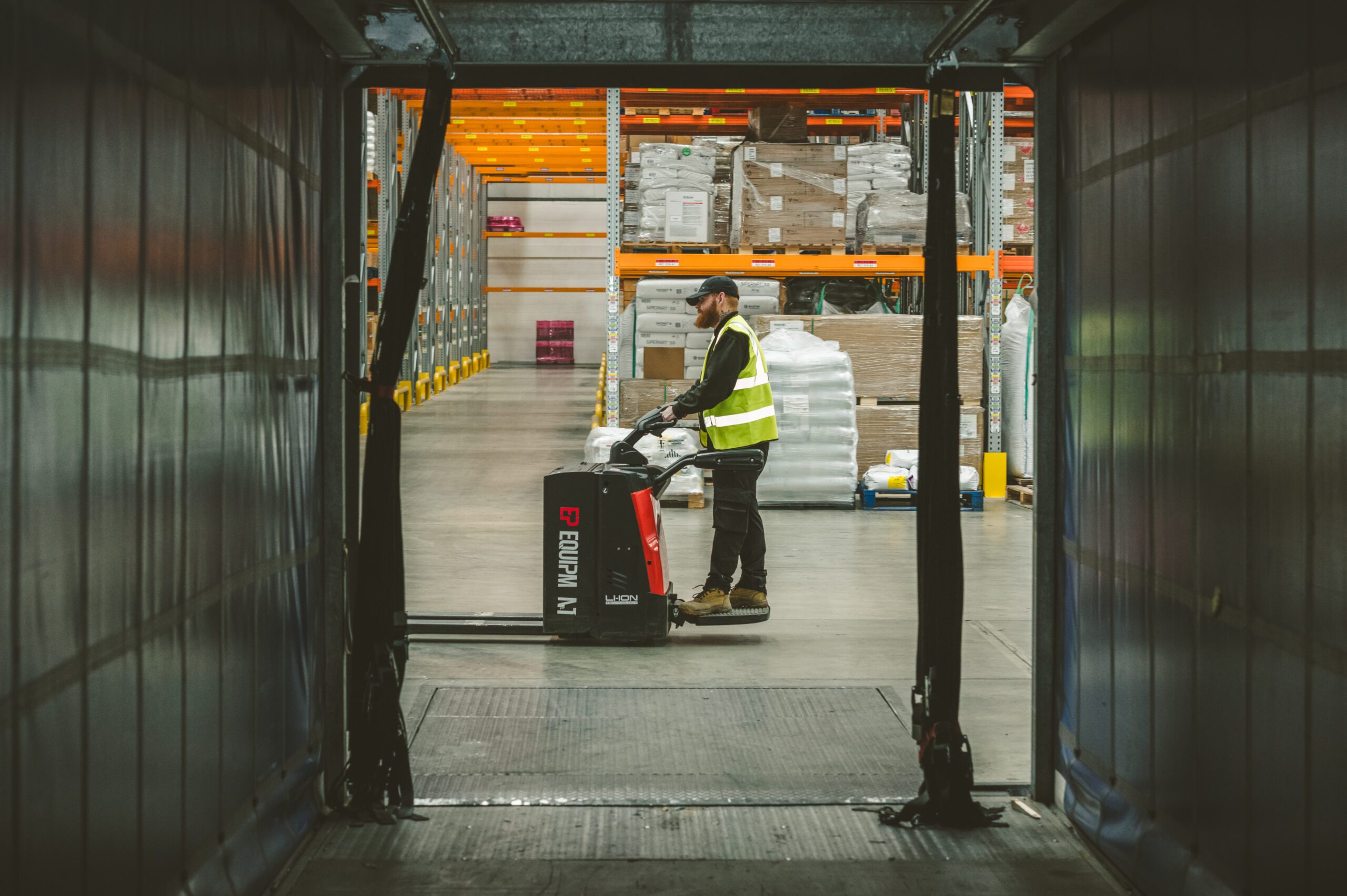
LATEST BLOGS
Bonded Warehouse or Green Warehouse – Exploring John K Philips’ Storage Solutions
Choosing the right warehousing solution can ma…
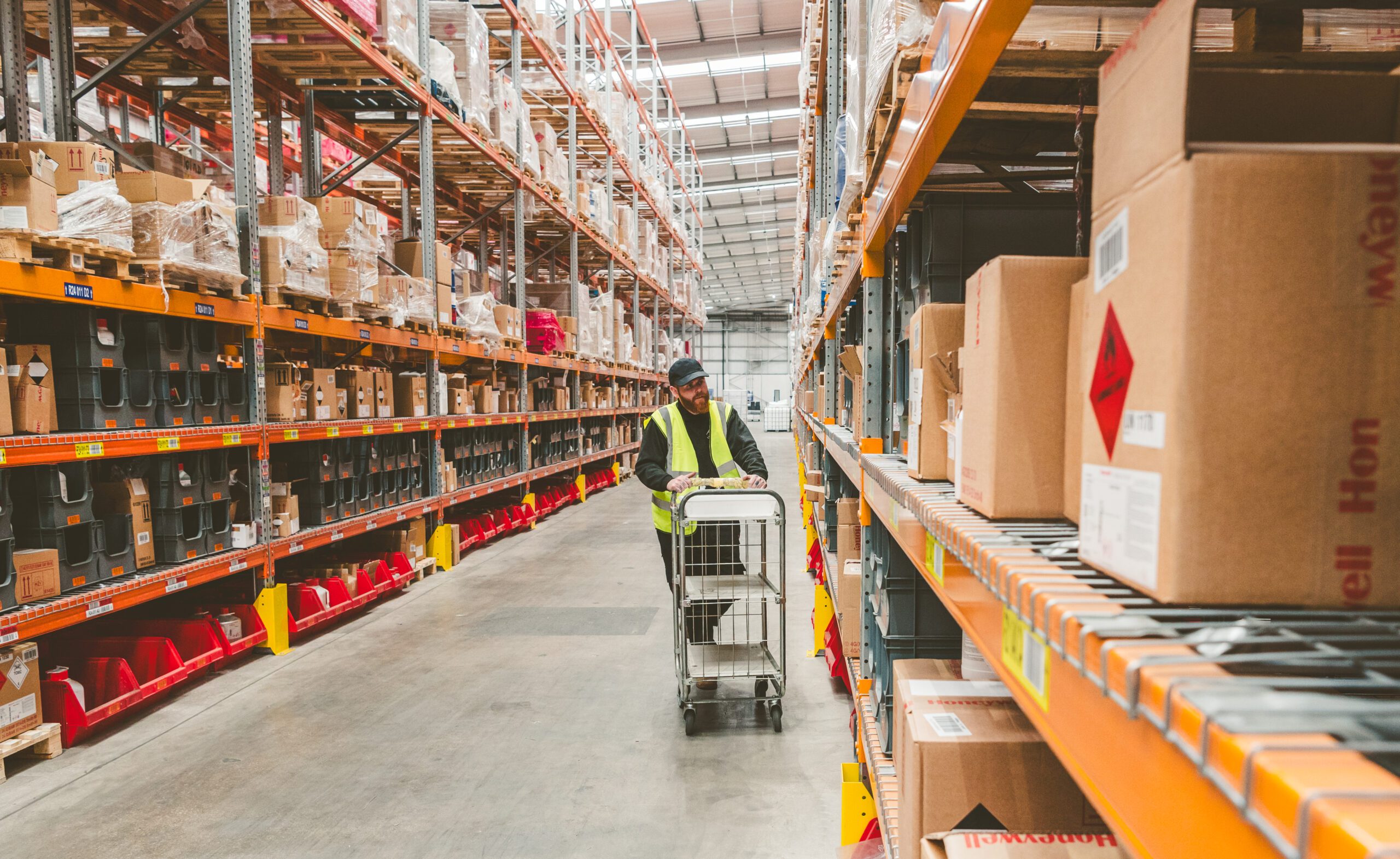
LATEST BLOGS
The best strategies for pick and pack
In the fast-paced world of warehousing and logi…
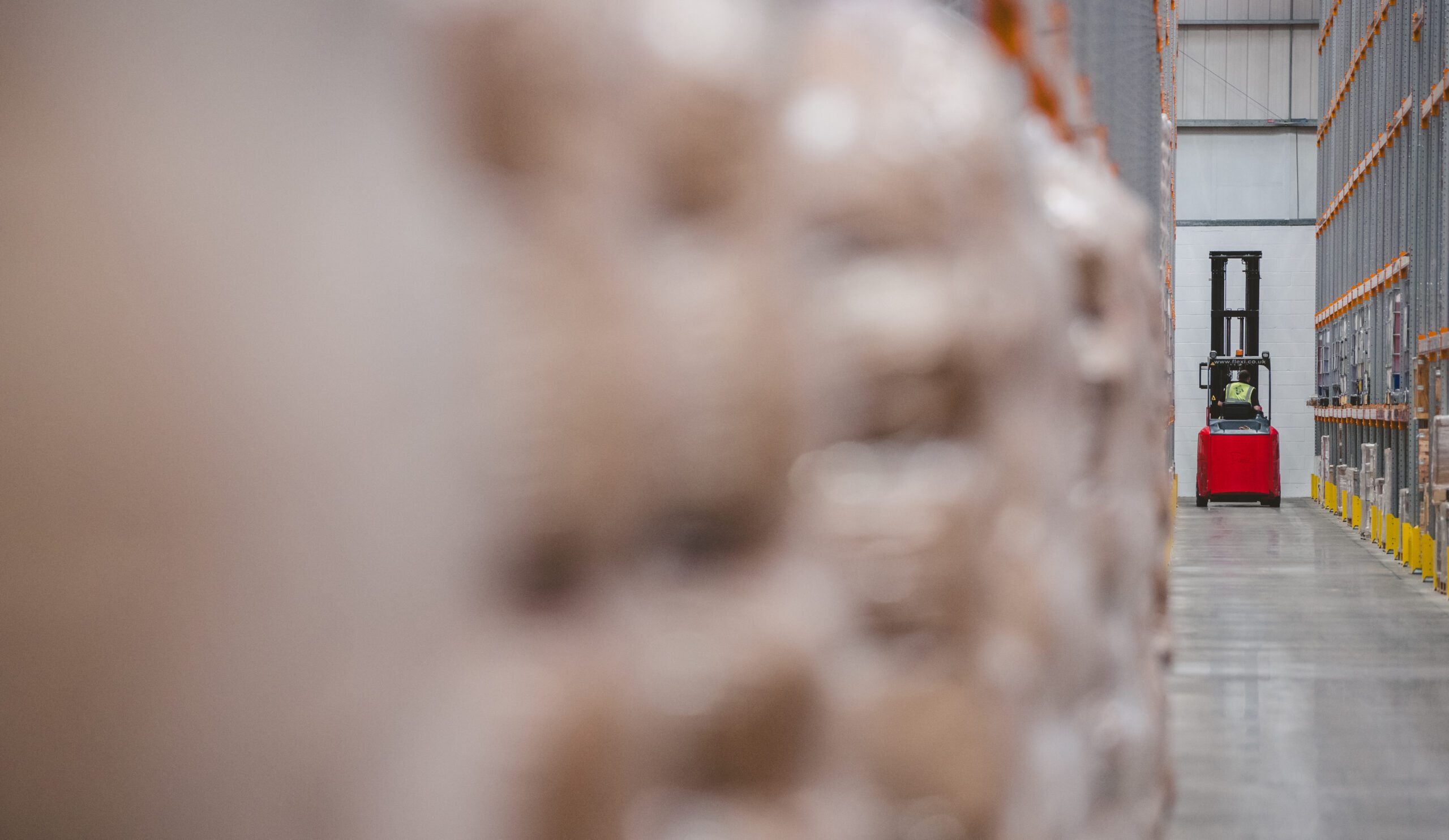
LATEST BLOGS
How can your business benefit from green warehousing in 2025?
Sustainability remains a critical component o…
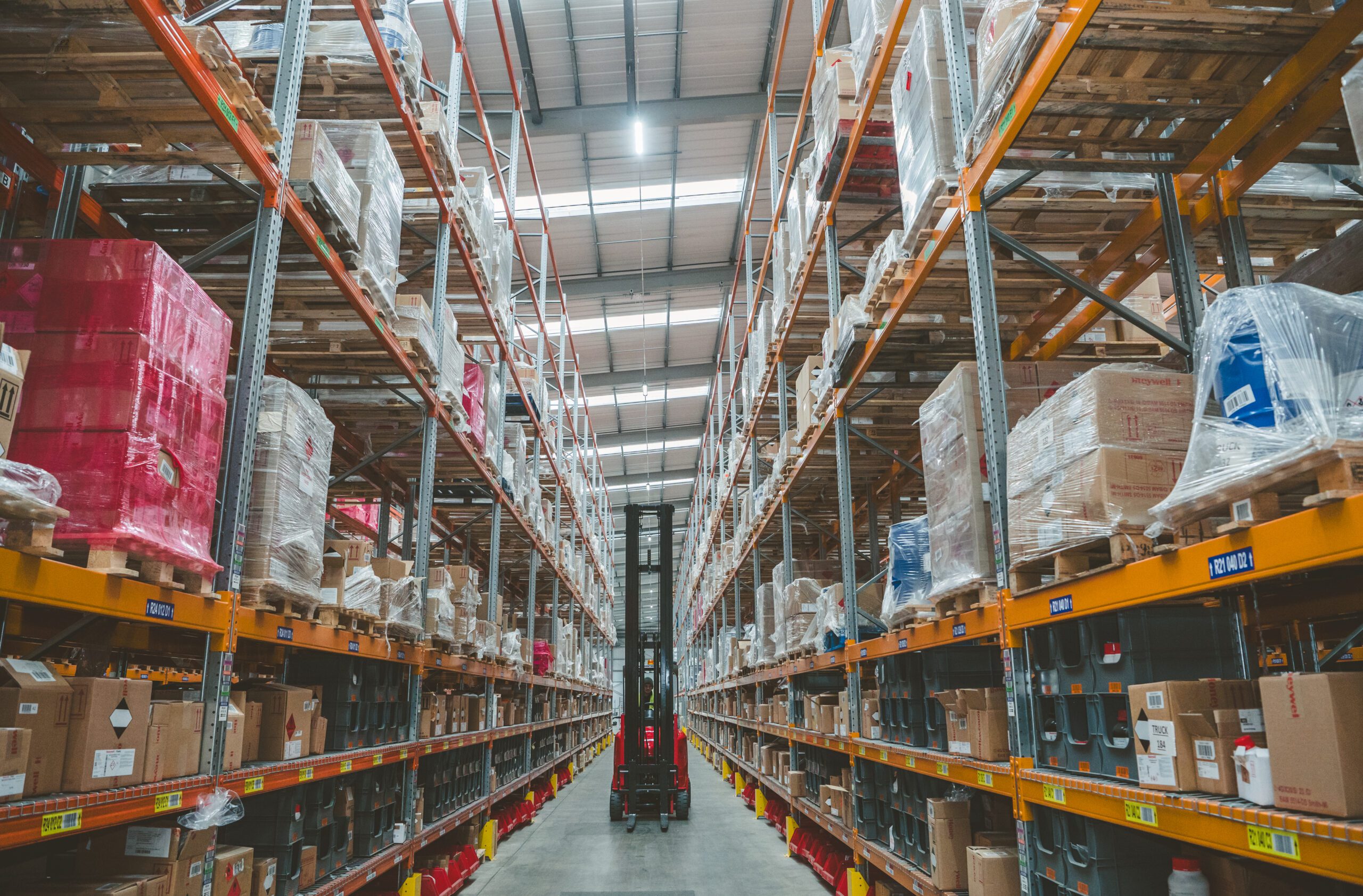
LATEST BLOGS
4 ways green warehouses are shaping the future
Now more than ever, businesses from all over the …
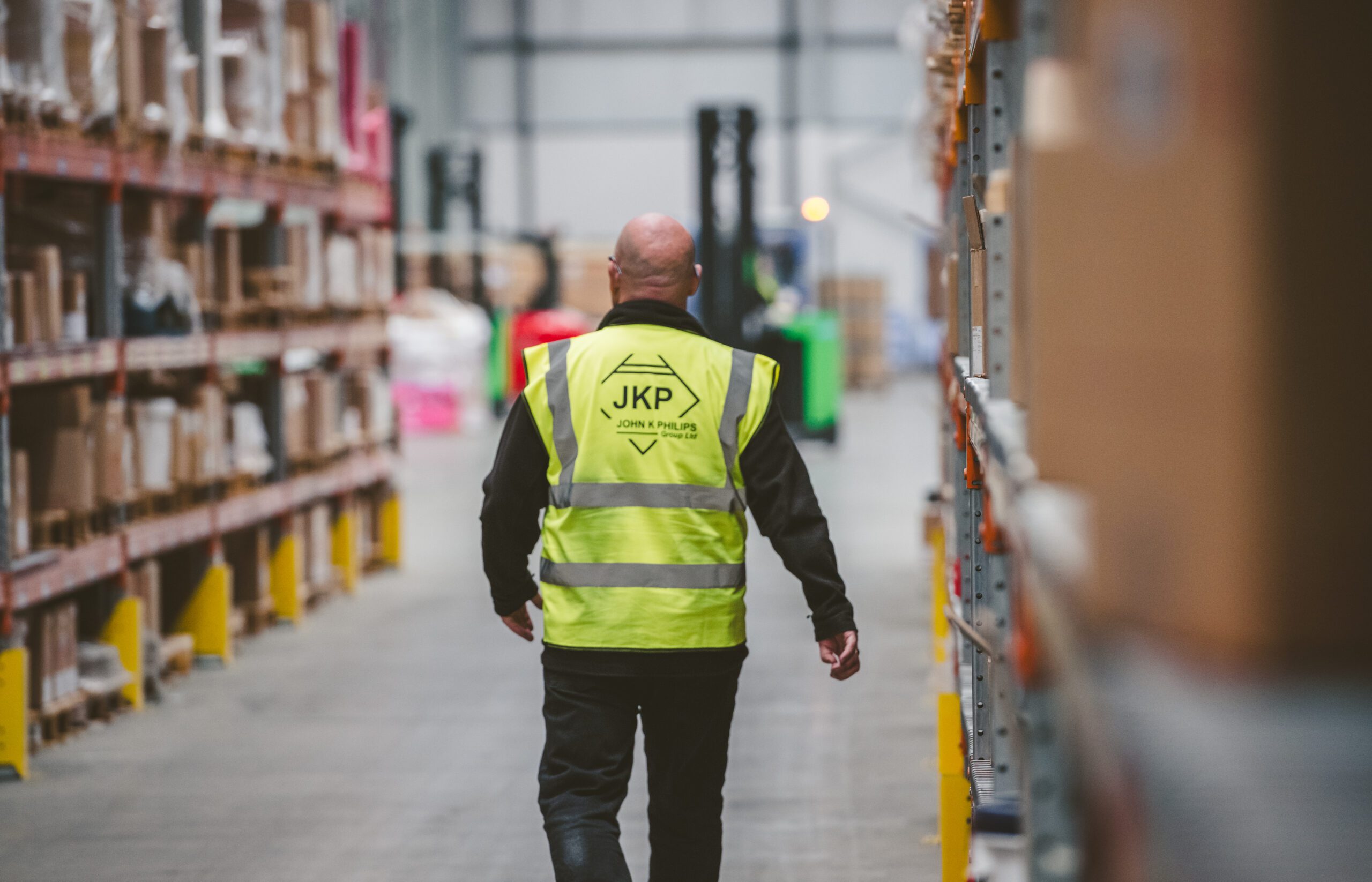
LATEST BLOGS
How to choose the right pick and pack service
Whether you’re a small start-up and need some ad…
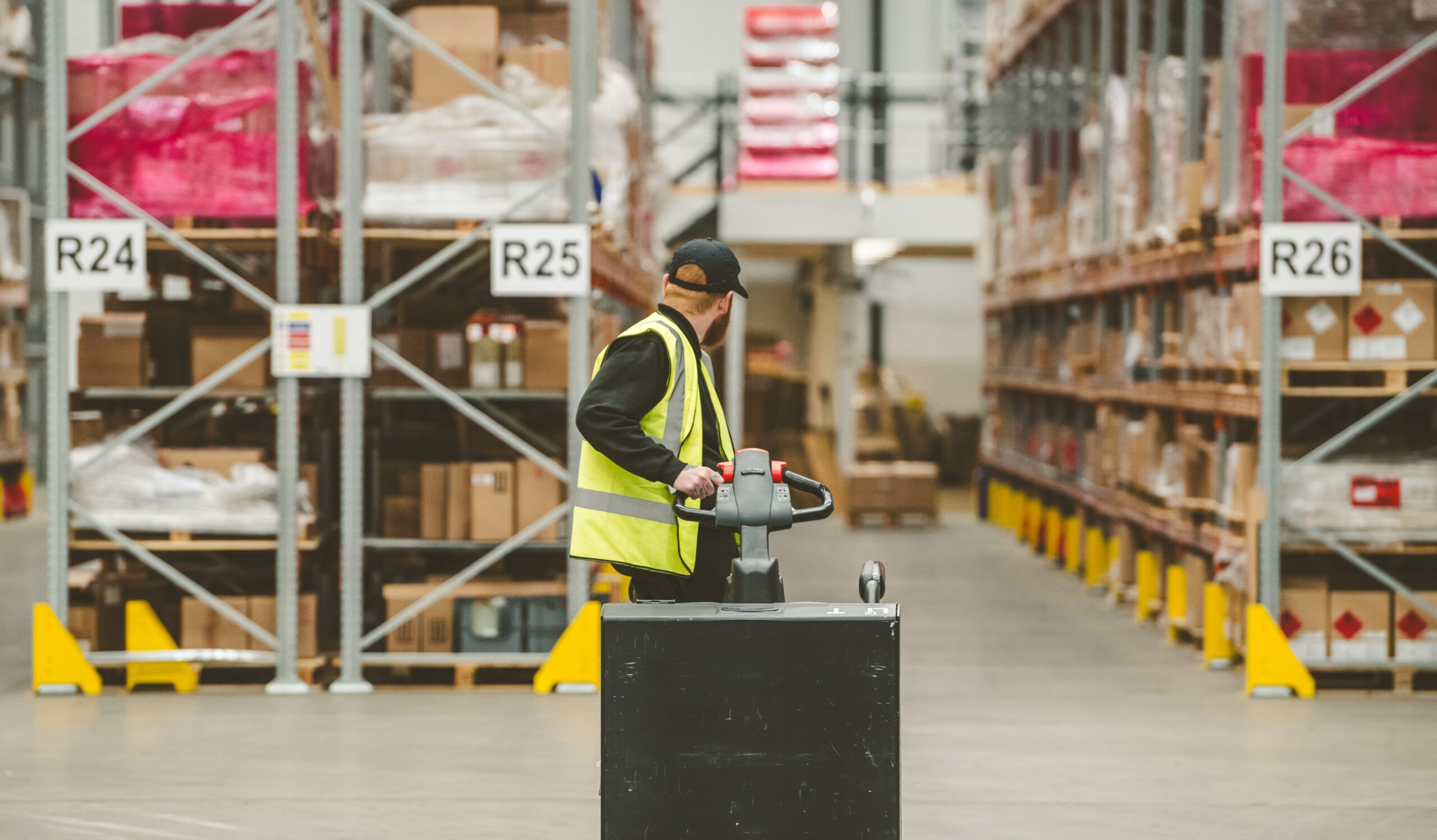
LATEST BLOGS
What is a bonded warehouse and why should you use one?
Do you import and export goods outside of the UK m…